Custom Rotational Molding
Pipeline Stands
Award of Distinction for Innovation 2021 from Alberta Farm Animal Care Council
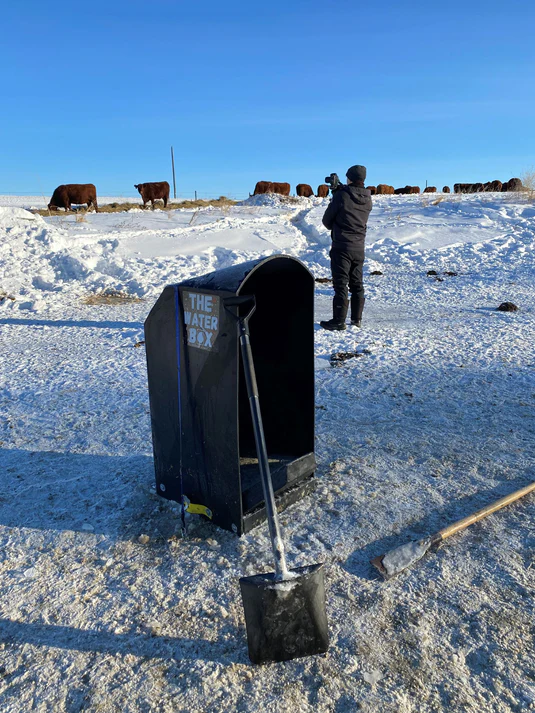
The Water Box™ is intended for direct watering from an available water source such as a dugout, slough, slow moving creek, etc. during the winter months. The Water Box™ is inserted through the ice surface of a desired water source, froze in and then self-utilized by livestock for 24-hour accessible drinking water. Livestock access the water source by lifting the nose flipper located on The Water Box™ lid then place their heads into the watering receptacle to drink.
Emax Plastics is the Exclusive Manufacturer of The Water Box
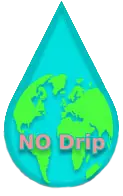
Custom Molding with AquaMax
A branch of Emax Plastics, AquaMax has exclusive rights to the floating dock kits, floating dock plans and navigation buoys
No Drip
Our badge of honor that symbolizes our Recycle Program and our commitment to a greener, safer work environment. Our No Drip products include Spill Trays, which provide our customers with the durability they would expect.
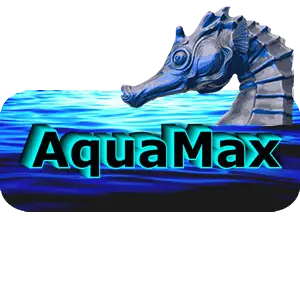
Why Choose Emax Plastics for Rotational Molding?
If you’re in search of a reliable rotational molding company, Emax Plastics is your ideal partner. With over four decades of experience, we have upheld our core values and earned the trust of innovative multi-national companies. The end-users of some of our products include Halliburton, Shell, Dow Chemical, Traction, Suncor Energy, Conoco Phillips, CNRL, United Rentals, Napa, Sherritt, Cross Country, and Schlumberger. Our commitment to bringing our clients’ visions to life has enabled us to create high-quality rotationally molded plastic products through creative design, cutting-edge biaxial rotational molding machines, and the industry’s finest resins.
Product Development
Finding an experienced roto molding company can be a challenge. At Emax Plastics, our team of experts will guide you from the initial concept through 3D design to a fully assembled prototype. We ensure that your product is designed for efficient rotational molding production from concept to completion.
Rotational Molding
Emax Plastics possesses the capability to produce 500,000 units annually. We utilize lean manufacturing principles to efficiently meet your assembly and post-operation requirements. Contact us today to [request a quote](#contact-us) and make us your trusted partner for all your rotational molding needs.
What is Rotational Molding?
Rotational molding, also known as rotomolding, is a plastic forming process that is used to create hollow plastic products with a variety of shapes and sizes. This manufacturing process involves several key steps and offers numerous advantages, which have contributed to its popularity over the years.
Rotational Molding Process
1. Loading the Mold: The first step involves prepping the mold and adding pulverized polyethylene (we purchase Linear Low Density Polyethene in powdered form, but we pulverize and granulate our recycled products) and load it into a mold. The mold is then sealed to prevent any powder from escaping.
2. Heating and Rotating the Mold: The mold is heated by green natural gas while being rotated on two or more axes. The heat causes the polyethylene to adhere to the mold walls. The rotation at different speeds ensures that the polymer spreads evenly throughout the mold, resulting in a seamless, strong polished finish.
3. Cooling the Mold: After the heating process, the mold is cooled using fans until it can be safely handled. During cooling, the newly formed plastic part will shrink, making it easier to remove from the mold.
4. Mold Removal: A mold release agent (MRA) is often used to aid in the removal of the mold from the new product.
5. Finishing: Additional finishing processes include detailing and clean up, to enhance the product’s accuracy, consistency, and appearance.
6. Warehousing and Drop Shipping: Manufacturers like Emax Plastics may offer warehousing and drop shipping services for the products, allowing for efficient storage and distribution.
Advantages of Rotational Molding
1. Durability: Rotomolded plastic products are highly durable, impact resistant, seamless and can withstand a wide range of environmental conditions. They are UV enhanced, making them more durable than most other materials and are resistant to corrosion, rust or deterioration.
2. Cost-Effective: Rotomolded products are lightweight, which reduces shipping costs. Additionally, the manufacturing process itself is relatively cost-effective, especially for larger and bulkier items. Our Navigational Buoys are designed specifically without weights or cement, making their handling, shipping and storage costs even more cost effective than our competitors.
3. Design Flexibility: Rotomolding allows for design flexibility, including specifying wall thickness. It also enables the inclusion of molded logos, eliminating the need for product stickers that may peel over time.
4. Long and Short Productions: Rotomolding is suitable for long and short production runs (20-15,000 pieces).
5. Low Tooling Costs: Compared to some other plastic manufacturing processes, rotomolding typically has lower tooling costs, as it doesn’t require complex molds or extensive machining.
6. Environmentally Friendly: Rotomolding produces minimal waste, and any excess material can be recycled, making it an environmentally friendly plastic manufacturing method.
Why Partner With Emax Plastics?
When seeking a rotational molding company, Emax Plastics stands out for its reputation as an industry expert and its commitment to customer satisfaction. We maintain a transparent and communicative culture, have created a recycling program to minimize waste, and offer cost savings and improved lead times. Our primary goal is to deliver products on time, as specified, and with uncompromising quality. Our team will collaborate with you to ensure efficient project flow and realistic expectations.
Rotational molding is a versatile plastic forming process that offers a range of advantages, including durability, cost-effectiveness, design flexibility, and the ability to create large quantities of product with warehousing storage for effecient distribution. These characteristics make it a preferred method for manufacturing a wide variety of plastic products, such as those produced by Emax Plastics.
Emax Plastics is your trusted partner for rotational molding, offering a combination of experience, quality, value and innovation to bring your plastic product ideas to life.


You May Have Rented Our Products Before
Why not have one designed for your specific application? Our submersible Floating Platforms can be custom designed and built to accommodate any size and/or weight of pump.
Simply the Best Design for the Oilfield!