Spill Containment Trays & Drip Pans Wholesale
Introduction to Spill Containment Tray Solutions
In today’s fast-paced and regulation-driven workplaces, maintaining a clean, safe, and compliant environment is not just a priority—it’s a necessity. Among the many tools and strategies employed to achieve this goal, spill containment trays and drip pans stand out. They are simply design, effective, and versatile. These essential safety products are designed to manage and contain leaks, drips, and spills. These spills can occur during the storage, handling, and transfer of liquids, thereby preventing workplace accidents, environmental contamination, and regulatory fines.
We Have 18 Sizes & Capacities
10 or More Spill Containment Trays for Sale at Wholesale Prices
Spill Containment Trays generally come in Black, but you can order different colored trays. They come with a minimum order of 10 units per color. Please call us for any color other than black.
White trays are Virgin Grade (Food Grade) and are an additional fee.
Our Spill Containment Trays are represented with our No Drip logo, providing you with consistent, high quality No Drip Assurance and Satisfaction
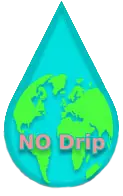
Spill Containment Tray Details
Overview of different models, weight, gallons it will hold, size and retail pricing (shown in Canadian here, but US prices are above, and will also be reflected in the cart. The cart should reflect the country you are in.)
Model # | LBS | GAL | Size L x W x H | Retail | |
---|---|---|---|---|---|
Spill Tray 12 | 8 | 12 | 24” x 36” x 4” | $69.12 | |
Spill Tray 20 | 11 | 20 | 24” x 61” x 4” | $95.04 | |
Spill Tray 15 | 8 | 15 | 24” X 24” X 7” | $69.12 | |
Spill Tray 21 | 10 | 21 | 36” X 24” X 7” | $92.45 | |
Spill Tray 28 | 11 | 28 | 48” X 24” X 7” | $101.69 | |
Spill Tray 30 | 13 | 30 | 36″ X 36″ X 7″ | $120.18 | |
Spill Tray 45 | 14 | 45 | 48” X 36” X 7” | $113.25 | |
Spill Tray 55 | 16 | 55 | 60” X 36” X 7” | $129.43 | |
Spill Tray 90 | 30 | 90 | 42” X 84” X 6” | $242.68 | |
Spill Tray 100 | 32 | 110 | 46” X 38” X 12” | $258.85 | |
Spill Tray 115 | 35 | 115 | 54” x 54” x 10” | $283.12 | |
Spill Tray 125 | 35 | 125 | 60” X 84” X 7” | $283.12 | |
Spill Tray 130 | 55 | 130 | 51” X 82” X 9” | $381.35 | |
Spill Tray 195 | 65 | 190 | 102” X 72” X 7” | $544.29 | |
Spill Tray 210 | 90 | 210 | 92” X 68” X 11” | $544.29 | |
Spill Tray 350 | 135 | 300 | 98” X 77” X 18” | $719.94 | |
Spill Tray 1100 | 425 | 1100 | 140” X 98” X 26” | $2,158.88 | |
Spill Tray 1100/400 | 400 | 1100 | 179” X 98” X 23” | $2,158.88 |
Our Product Range
Incorporating Our Spill Containment Trays into Your Workplace
At the forefront of workplace safety and environmental stewardship, our comprehensive selection of spill containment trays and drip pans offers unparalleled protection against leaks, spills, and the consequent hazards they pose. Our products are meticulously designed to cater to a wide array of industries, including:
- Oil and Gas Facilities
- Manufacturing Plants
- Chemical Processing Plants
- Automotive Industry
- Agriculture and Pesticide Use
- Transportation and Storage Facilities
- Pharmaceuticals
- Restaurant and Food Processing Facilities
Ensuring a cleaner, safer, and more compliant operational environment. Below, we detail our diverse product range, showcasing how each variant stands to benefit your facility’s specific needs.
Implementing our spill containment solutions into your operations not only enhances safety and compliance but also streamlines cleaning and maintenance processes. Ideal for containing leaks, preventing waste leakage, and managing substance spills, our trays and pans are essential for any facility looking to mitigate risks and protect its workforce.
Whether you’re upgrading your existing spill containment measures or setting up a new facility, our diverse product range offers the flexibility, reliability, and quality you need to ensure a safe and efficient workplace. With options for every industry and application, from spill control in labs to storage pad protection, our spill containment solutions are designed to meet the challenges of modern workplaces. Choose from our selection to enhance your facility’s safety and environmental compliance today.
Features and Benefits of Spill Containment Trays
Our spill containment products are designed with precision, incorporating a range of features that stand at the forefront of industry standards for safety and environmental care. By understanding the core features of our spill containment trays and drip pans, customers can better appreciate the significant benefits these solutions offer to their operations. Here’s a deep dive into the key features and the corresponding benefits our products deliver.
Features
- Made from recycled materials. See our Recycle Program.
Durable and resistant to a wide range of chemicals. This durability ensures that spills are contained reliably over time, even in high-traffic areas or during rough handling.
- Impact Resistance: Engineered to withstand drops, knocks, and other impacts, our trays ensure continued performance and longevity, even in the toughest workplaces.
- Available in Various Sizes and colors (with minimum order) to accommodate different volumes and applications.
- Climate Friendliness: Our trays are unaffected by the weather. Heat resistant and can withstand the freezing snow, still pliable at 30 degrees below.
- Reduces cleanup costs and time: Protects surrounding environment and resources.
- Made with Linear Low-Density Polyethylene (LLDPE): Our polyethylene, LLDPE, spill trays are the workhorses of spill containment. Known for their robustness, these trays can handle everything from oil and chemicals to water and other liquids. Their resilience against impacts and environmental stress cracks makes them suitable for harsh industrial environments where durability is key.
- Eco-Friendliness: With a focus on sustainability, our products are made from recyclable materials, supporting your company’s green initiatives.
Benefits
- Enhanced Workplace Safety: By effectively containing spills and leaks, our products significantly reduce the risk of slip-and-fall accidents, ensuring a safer environment for employees and visitors alike.
- Prevents accidents and injuries: Creates a safer work atmosphere
- Compliance with Regulations: Our spill containment solutions are designed to help facilities comply with local, state, and federal environmental and safety regulations, avoiding potential fines and legal issues.
- Aids in meeting OSHA and EPA guidelines: Supports compliance efforts with ease.
- Prevention of Waste Leakage: By capturing spills and leaks efficiently, our products minimize waste and prevent the contamination of surrounding areas, contributing to a more sustainable operation.
- Pliability: Unlike rigid materials that can crack under pressure, our trays offer a degree of flexibility, absorbing impacts without compromising their integrity.
- Protection of Storage Areas: Our trays and pans safeguard storage areas and surfaces from damage caused by leaks and spills, preserving the integrity of facility infrastructure and equipment.
- Extends the lifespan of storage facilities and equipment: Keeps storage areas clean and well-maintained
- Nestable Stacking: Designed for efficient storage and transport, our trays can be easily nested and stacked, saving valuable space in your facility.
The versatility and efficiency of our spill containment trays and drip pans make them indispensable across a wide range of settings. From laboratories to industrial sites and food processing facilities, these products play a pivotal role in ensuring safety, cleanliness, and compliance. Below, we explore various applications and use cases that highlight the adaptability and effectiveness of our spill containment solutions
Examples of Industry Use Cases
Industrial sites use spill trays for a variety of reasons, mainly to manage and contain leaks, drips, and spills of chemicals, oils, fuels, and other hazardous or non-hazardous liquids. These trays are essential components of workplace safety and environmental protection strategies. The types of industrial sites that commonly use spill trays include but are not limited to:
Oil and Gas Facilities
In the Oil and Gas industry, a Site Manager at an Oil Refinery is a prime example of someone who would use spill containment trays as part of their daily operations. The Site Manager is responsible for overseeing the refinery’s operations, ensuring that all processes are conducted safely, efficiently, and in compliance with environmental regulations. Here’s how they might use spill containment trays:
- Maintenance and Repair Work: During routine maintenance or repair of refinery equipment, such as pumps, valves, and pipelines, spill containment trays are placed underneath the work area to catch any oil or chemical leaks. This practice prevents the substances from contaminating the ground or water sources and makes cleanup easier and safer.
- Fuel Transfer Areas: The Site Manager ensures that spill containment trays are used in areas where fuels are transferred from one container to another or from tankers to storage tanks. These trays catch any spills during the transfer process, reducing the risk of soil and water pollution.
- Chemical Storage: The refinery stores various chemicals used in the refining process. Spill containment trays are placed under storage containers or drums to catch leaks, preventing ground contamination and reducing the risk of chemical reactions or fire hazards.
- Waste Disposal Areas: The Site Manager uses spill containment trays in areas designated for the temporary storage of hazardous waste before it is properly disposed of. This minimizes the risk of environmental contamination and helps comply with waste management regulations.
- Emergency Spill Response: In the event of an accidental spill, the Site Manager coordinates the emergency response efforts, which include the use of larger spill containment solutions, like trays and berms, to quickly contain and mitigate the impact of the spill.
By integrating spill containment trays into the refinery’s operational and safety protocols, the Site Manager plays a crucial role in protecting the environment, ensuring the safety of the workforce, and maintaining compliance with regulatory standards. This proactive approach to spill management is critical in minimizing the environmental footprint of oil and gas operations.
Transportation and Storage Facilities
Warehouses and distribution centers that handle liquid goods use spill trays under stored containers or during the transfer of liquids to contain accidental spills. In the Transportation and Storage Facilities sector, a Warehouse Manager responsible for the operation of a warehouse that stores and handles hazardous materials, chemicals, or other liquid goods is an excellent example of someone who would use spill containment trays as part of their operational protocols. The Warehouse Manager ensures that products are stored safely, prevents contamination or damage to the stored goods, and complies with environmental and safety regulations. Here’s how they might use spill containment trays:
- Chemical Storage Areas: Spill containment trays are placed under shelves or pallets where chemicals are stored, especially those in drums, barrels, or smaller containers. This is to catch any leaks or spills, preventing hazardous materials from contaminating the warehouse floor or seeping into the environment.
- Loading and Unloading Zones: During the loading and unloading of hazardous liquids, spill containment trays are used to catch any spills that occur when containers are being moved on or off transportation vehicles. This practice minimizes the risk of slip hazards and environmental pollution.
- Fuel Storage and Dispensing Areas: For warehouses that have on-site fuel storage for vehicles or backup generators, spill containment trays are placed under fuel tanks and dispensing areas. This ensures any leaks or spills are contained, reducing the risk of fire hazards and soil or water contamination.
- Battery Charging Stations: Warehouses often have battery charging stations for forklifts and other electrically powered equipment. Spill containment trays are used to catch any acid leaks from batteries, protecting workers from exposure and preventing floor damage.
- Liquid Packaging and Repackaging Areas: In facilities where liquids are packaged or repackaged, spill containment trays are used under filling stations or packaging tables to catch any overflows or spills, ensuring that the product quality is maintained and reducing waste.
- Waste Handling Areas: Spill containment trays are also utilized in areas designated for the collection and temporary storage of hazardous waste, including used chemicals, oils, and other contaminants. This prevents leaks and spills from hazardous waste, ensuring safe and compliant waste management practices.
By integrating spill containment trays into various areas of warehouse operations, the Warehouse Manager not only enhances the safety of the workplace but also plays a vital role in environmental protection. This proactive approach to managing spills and leaks helps in maintaining compliance with regulatory requirements and demonstrates a commitment to responsible materials handling and storage.
Manufacturing Plants
In the Manufacturing Plant industry, a Production Line Supervisor at a facility that manufactures chemicals, paints, or similar products is a prime example of someone who would use spill containment trays as part of their daily operations. The Production Line Supervisor is responsible for overseeing the smooth operation of the production line, ensuring that products are manufactured efficiently, safely, and in compliance with all relevant health and safety and environmental regulations. Here’s how they might use spill containment trays:
- Chemical Mixing and Processing Areas: The supervisor ensures that spill containment trays are placed beneath mixing vats, processing equipment, and pipelines to catch any accidental spills or leaks of chemicals, solvents, or other hazardous materials. This is crucial for preventing workplace accidents and environmental contamination.
- Assembly Lines: In areas where products or components are assembled and might involve the use of adhesives, paints, or small amounts of chemicals, spill containment trays are used to catch drips and spills. This practice keeps the work area clean and reduces the risk of slips and falls.
- Storage and Handling of Raw Materials: The Production Line Supervisor ensures that spill containment trays are used in storage areas and during the handling of liquid raw materials or hazardous substances. These trays prevent leaks from contaminating the facility and reduce the risk of fire hazards in areas storing flammable materials.
- Filling and Packaging Stations: In facilities where products are filled into containers, spill containment trays are placed under filling stations to catch overflows or spills. This helps in maintaining product quality, reduces waste, and ensures a cleaner work environment.
- Maintenance and Equipment Cleaning Areas: The supervisor uses spill containment trays under machinery during maintenance or cleaning operations. These trays catch any residual chemicals or fluids, preventing them from contaminating the facility.
- Waste Collection Areas: Areas designated for the collection of hazardous waste or used chemicals are equipped with spill containment trays to contain any leaks from waste containers, thereby ensuring that waste is handled in a safe and environmentally responsible manner.
By implementing the use of spill containment trays, the Production Line Supervisor plays a critical role in enhancing workplace safety, protecting the environment, and ensuring compliance with regulatory requirements. This approach helps in managing the risks associated with the handling and processing of hazardous materials and contributes to the overall efficiency and safety of the manufacturing operation
Laboratory Industry
In the Laboratory Industry, a Laboratory Manager responsible for overseeing the operations of a research or clinical lab is a prime example of someone who would use spill containment trays as part of their day-to-day activities. The Laboratory Manager ensures that the laboratory operates safely, efficiently, and in compliance with all relevant health, safety, and environmental regulations. Here’s how they might use spill containment trays:
- Chemical Handling and Storage: Spill containment trays are used in areas where chemicals are stored and handled to catch any accidental spills or leaks. This is crucial for preventing hazardous substances from contaminating work surfaces, reducing the risk of exposure to lab personnel, and preventing environmental contamination.
- Experiment Stations: During experiments or procedures that involve the use of liquids, including chemicals, reagents, and biological samples, spill containment trays are placed under apparatus or reaction setups. This helps in containing spills, facilitating easy cleanup, and maintaining a safe working environment.
- Sample Preparation Areas: In areas where samples are prepared for analysis or testing, spill containment trays catch spills of potentially hazardous or infectious materials. This is particularly important in clinical labs where the samples may pose a biological hazard.
- Equipment Maintenance and Cleaning: Spill containment trays are used under laboratory equipment during maintenance, cleaning, or calibration activities to catch any fluids that may leak out. This includes equipment like centrifuges, spectrophotometers, and chromatography systems.
- Waste Disposal Stations: Laboratories generate various types of hazardous waste, including chemical, biological, and radioactive waste. Spill containment trays are used in waste disposal areas to contain leaks from waste containers, preventing contamination and ensuring safe disposal practices.
- Solvent Dispensing Areas: In labs where solvents are regularly dispensed, spill containment trays are placed underneath dispensing areas to catch drips or spills. This reduces the risk of fire hazards and exposure to volatile organic compounds.
By implementing the use of spill containment trays, the Laboratory Manager plays a crucial role in enhancing the safety and environmental compliance of the laboratory. This approach helps in managing the risks associated with the handling and disposal of hazardous materials and contributes to creating a safer work environment for laboratory personnel while protecting the environment.
Chemical Processing Plants
In the Chemical Processing Plants industry, a Process Engineer responsible for designing, implementing, and optimizing chemical processes is a key example of someone who would use spill containment trays as part of their daily responsibilities. The Process Engineer is involved in ensuring that chemical reactions and processing operations are conducted safely, efficiently, and in compliance with environmental and safety regulations. Here’s how they might use spill containment trays:
- Chemical Reaction and Synthesis Areas: The Process Engineer designs reaction vessels and synthesizing areas to include spill containment trays that catch any accidental leaks or spills of reactive chemicals. This is crucial for preventing hazardous chemical exposures and environmental contamination.
- Pilot Plant Operations: During the scale-up of chemical processes from the laboratory to pilot plant scale, the Process Engineer ensures that spill containment trays are used under experimental setups. These trays are essential for containing spills during the testing of new processes or chemical reactions, thereby safeguarding both personnel and the facility.
- Solvent Dispensing and Mixing Zones: In areas where solvents are dispensed and mixed, the Process Engineer incorporates spill containment trays to capture any accidental releases. This practice helps in minimizing the risk of fire hazards and reducing volatile organic compound (VOC) emissions into the atmosphere.
- Material Transfer Points: The engineer ensures that spill containment trays are placed at material transfer points, where chemicals are moved from one container to another or from storage tanks to reaction vessels. This strategy prevents spillage and contamination of the plant floor, aiding in cleaner and safer operations.
- Equipment and Storage Areas: The Process Engineer designs equipment and storage areas to include spill containment solutions, such as trays under storage tanks, drums, and totes, to catch leaks and prevent ground and water pollution.
- Laboratory and R&D Areas: In research and development laboratories where new chemical products or processes are developed, spill containment trays are used under experimental setups to ensure that any spills are contained, making it easier to maintain a safe and clean working environment.
- Waste Handling and Disposal Areas: The Process Engineer is responsible for designing waste handling systems that include spill containment trays in areas where chemical waste is stored temporarily before disposal. This minimizes the risk of environmental contamination and ensures compliance with waste management regulations.
By incorporating spill containment trays into chemical processing operations, the Process Engineer not only enhances workplace safety and environmental protection but also contributes to the efficiency and sustainability of chemical manufacturing processes. This careful management of chemical handling and processing is essential for minimizing the industry’s environmental impact and ensuring the safety of workers and surrounding communities.
Pharmaceutical Industry
In the Pharmaceutical Industry, a Quality Assurance (QA) Manager responsible for ensuring that pharmaceutical products are manufactured, stored, and handled in accordance with regulatory standards and company quality policies is a key example of someone who would use spill containment trays as part of their daily responsibilities. The QA Manager plays a crucial role in maintaining product safety, efficacy, and compliance with health regulations. Here’s how they might use spill containment trays:
- Manufacturing Areas: In areas where active pharmaceutical ingredients (APIs) are processed or pharmaceutical products are formulated, spill containment trays are used under mixing tanks, formulation equipment, and processing lines. This is to catch any spills or leaks of APIs, solvents, or other hazardous materials, ensuring that manufacturing areas remain uncontaminated and safe for workers.
- Laboratories: During the development and quality control stages, laboratories use various chemicals and reagents. Spill containment trays are placed under laboratory benches, equipment, and storage cabinets to contain any accidental spills, thereby protecting laboratory personnel and preventing contamination of samples or the laboratory environment.
- Drug Packaging Areas: In sections of the facility where drugs are packaged, spill containment trays are utilized beneath filling stations and along packaging lines to catch any product overflows or leaks. This helps in maintaining the integrity of the pharmaceutical products and reduces waste.
- Storage Facilities for Raw Materials and Finished Products: The QA Manager ensures that spill containment trays are used in storage areas holding raw materials, intermediates, and finished pharmaceutical products, especially those in liquid form or those that can leak. These trays prevent contamination of storage areas and help in maintaining the quality of the stored materials.
- Waste Disposal Areas: Pharmaceutical manufacturing generates waste, including excess chemicals and non-conforming products. Spill containment trays are used in waste handling areas to prevent leaks and spills from waste containers, facilitating safe and compliant disposal of pharmaceutical waste.
- Chemical and Reagent Dispensing Areas: Areas designated for the dispensing of chemicals and reagents used in manufacturing and testing processes are equipped with spill containment trays to catch drips or spills, ensuring that these materials are handled safely and in compliance with environmental regulations.
Automotive Industry
In the Automotive Industry, an Auto Repair Shop Owner is a perfect example of someone who would use spill containment trays as part of their daily operations. The shop owner is responsible for the maintenance and repair of vehicles, ensuring that services are provided efficiently and safely, while also complying with environmental regulations. Here’s how they might use spill containment trays:
- Oil Change Stations: Spill containment trays are placed beneath vehicles during oil changes to catch any oil that may spill. This prevents oil from contaminating the shop floor, reducing slip hazards and environmental impact.
- Fluid Dispensing Areas: When refilling or replacing vehicle fluids such as coolant, brake fluid, or transmission fluid, spill containment trays are used to catch any accidental overflows or spills. This helps in maintaining a clean work environment and prevents fluid waste from entering the drainage system.
- Battery Charging and Maintenance Areas: Batteries contain hazardous acids that can leak, so spill containment trays are used under batteries during charging, maintenance, or replacement to catch any leaks. This protects both the workers and the environment from hazardous substances.
- Parts Cleaning Stations: Parts cleaning stations often use solvents and degreasers to clean vehicle components. Spill containment trays are used under these stations to catch any spills or drips of cleaning fluids, preventing them from contaminating the shop floor or waterways.
- Vehicle Storage Areas: For vehicles that are leaking fluids and awaiting repair, spill containment trays are placed under these vehicles as a precautionary measure to collect any leaking fluids and prevent them from staining the floor or harming the environment.
- Workbench Areas: When mechanics work on small parts or engines at workbenches, spill containment trays can be used to catch small leaks or spills of oils, fuels, or other fluids. This makes cleanup easier and prevents hazardous materials from spreading.
By utilizing spill containment trays, the Auto Repair Shop Owner ensures a safer work environment for employees, minimizes environmental pollution, and adheres to regulatory standards regarding the handling and disposal of automotive fluids and hazardous materials. This proactive approach to spill management underscores the importance of safety and environmental responsibility in the automotive repair industry.
Agriculture and Pesticide Use
In the Agriculture and Pesticide Facilities industry, a Farm Manager overseeing a large agricultural operation is a key example of someone who would use spill containment trays as part of their daily management practices. The Farm Manager is responsible for the overall operation of the farm, including the safe and efficient use of pesticides and fertilizers to protect crops and increase yields. Here’s how they might use spill containment trays:
- Pesticide and Fertilizer Mixing Areas: When mixing pesticides or fertilizers, spill containment trays are used under mixing stations to catch any accidental spills or leaks. This prevents harmful chemicals from contaminating the soil and groundwater, ensuring a safer environment for workers and local wildlife.
- Storage Facilities for Chemicals: The Farm Manager ensures that all chemicals, including pesticides and fertilizers, are stored in areas equipped with spill containment trays. These trays catch leaks from containers, helping to prevent soil and water pollution and reducing the risk of accidental exposure to these chemicals.
- Refilling and Maintenance of Application Equipment: Before field application, equipment such as sprayers and spreaders are often filled and maintained in a central location. Spill containment trays are used during these processes to catch any spills of pesticides or fertilizers, minimizing the risk of environmental contamination.
- Waste Collection Points: The Farm Manager sets up designated areas for the disposal of empty chemical containers, non-reusable personal protective equipment, and other waste generated during the pesticide application process. Spill containment trays in these areas catch any residual chemicals, preventing them from entering the environment.
- Emergency Spill Response: In case of an accidental spill, the Farm Manager is responsible for initiating an immediate response to contain and clean up the spill, using spill containment trays and other materials to prevent the spread of chemicals and mitigate environmental damage.
By incorporating spill containment trays into the farm’s chemical handling and storage practices, the Farm Manager not only ensures compliance with environmental and safety regulations but also contributes to the sustainability and safety of the agricultural operation. This careful management of pesticides and fertilizers is crucial for protecting the ecosystem, farm workers, and the surrounding community from potential chemical exposure and pollution.
Restaurant and Food Processing Facilities
Crafted from high-quality, virgin food-grade materials, these spill trays are the epitome of purity and safety. Ideal for food processing environments and any setting where contamination control is essential, these trays ensure that integrity is never compromised.
Our virgin food-grade spill trays are designed for direct contact with food products, ensuring that any spills during processing or packaging are contained without risk of contamination. These trays support rigorous cleaning protocols and contribute to a hygienic processing environment, which is essential for meeting food safety standards.
In the Food Processing Facility and Restaurant industry, a Kitchen Manager or Executive Chef in a large restaurant or food processing plant is an excellent example of someone who would use spill containment trays as part of their daily operations. These professionals are responsible for overseeing the preparation, cooking, and presentation of food, ensuring that it meets safety standards, and managing the overall operation of the kitchen to ensure efficiency and compliance with health regulations. Here’s how they might use spill containment trays:
- Food Preparation Areas: Spill containment trays are used in areas where liquids such as oils, vinegars, sauces, and marinades are handled and prepared. These trays catch any spills, helping to maintain a clean and safe preparation area and preventing slips or falls caused by spilled liquids.
- Cooking Stations: In cooking areas, especially where deep fryers, boiling pots, or large-scale mixers are used, spill containment trays can catch overflow or spills of cooking oils, boiling water, or other hot liquids. This not only helps in maintaining cleanliness but also reduces the risk of burns or accidents.
- Chemical Storage Areas: Kitchens and food processing facilities store cleaning chemicals and sanitizers for equipment and surface cleaning. Spill containment trays under these storage areas prevent accidental leaks or spills of these chemicals, ensuring they do not contaminate food preparation surfaces or food products.
- Refrigeration and Thawing Areas: Trays can be placed under refrigeration units or in areas designated for thawing frozen ingredients to catch condensation or water runoff, preventing floor dampness that could lead to slips or the growth of bacteria.
- Waste Disposal Areas: Spill containment trays are useful in areas where organic waste or used cooking oil is collected before disposal or recycling. They help in containing leaks from waste containers, maintaining hygiene, and preventing attraction of pests.
By incorporating spill containment trays into their operations, Kitchen Managers or Executive Chefs not only ensure a cleaner, safer work environment but also help in preventing cross-contamination and maintaining high standards of food safety and hygiene. This practice is crucial for protecting the health of customers, complying with food safety regulations, and maintaining the efficiency of kitchen operations in food processing facilities and restaurants.
Ordering Information and Discounts for our Spill Containment Trays
Securing your workplace with top-quality spill containment trays and drip pans has never been easier. We offer a streamlined ordering process, competitive discount pricing for bulk purchases, and a range of customization options to ensure you get the most suitable solutions for your needs. Here’s everything you need to know about ordering from us and taking advantage of our special offers.
How to Order
- Online Ordering: Visit our website to browse our extensive product range. Our user-friendly online store allows you to select the spill containment solutions that best meet your needs, add them to your cart, and proceed to checkout. It’s fast, easy, and secure. You can reach us two ways! www.emaxplastics.ca or www.emaxplastics.com
- Customer Support: If you have questions or need assistance selecting the right product, our dedicated customer support team is here to help. You can reach out via phone or email. Call Travis at (780) 992-1793 or email us at emaxplastics@outlook.com. We pride ourselves on providing expert advice and support to ensure customer satisfaction.
- Custom Orders: For specific requirements, we offer customization options. Contact our sales team to discuss custom sizes, materials, or designs. We’re committed to providing solutions that perfectly fit your unique needs. See our Custom Molding section.
Special Offers and Discounts
- Bulk Order Discounts: We understand the importance of cost-effective solutions for businesses. That’s why we offer attractive discounts on bulk orders. Orders of more than 10 items qualify for special pricing, making it more affordable to equip your facility with high-quality spill containment solutions.
Significant savings on bulk purchases!
Ideal for outfitting entire facilities or stocking up on essential supplies!
- Promotional Offers: Keep an eye on our website and sign up for our newsletter to stay informed about promotional offers and additional discounts available throughout the year. These exclusive deals are our way of thanking our loyal customers.